What Is a Basic Oxygen Furnace? How Is Oxygen Used in Steelmaking?
Introduction to the Basic Oxygen Furnace
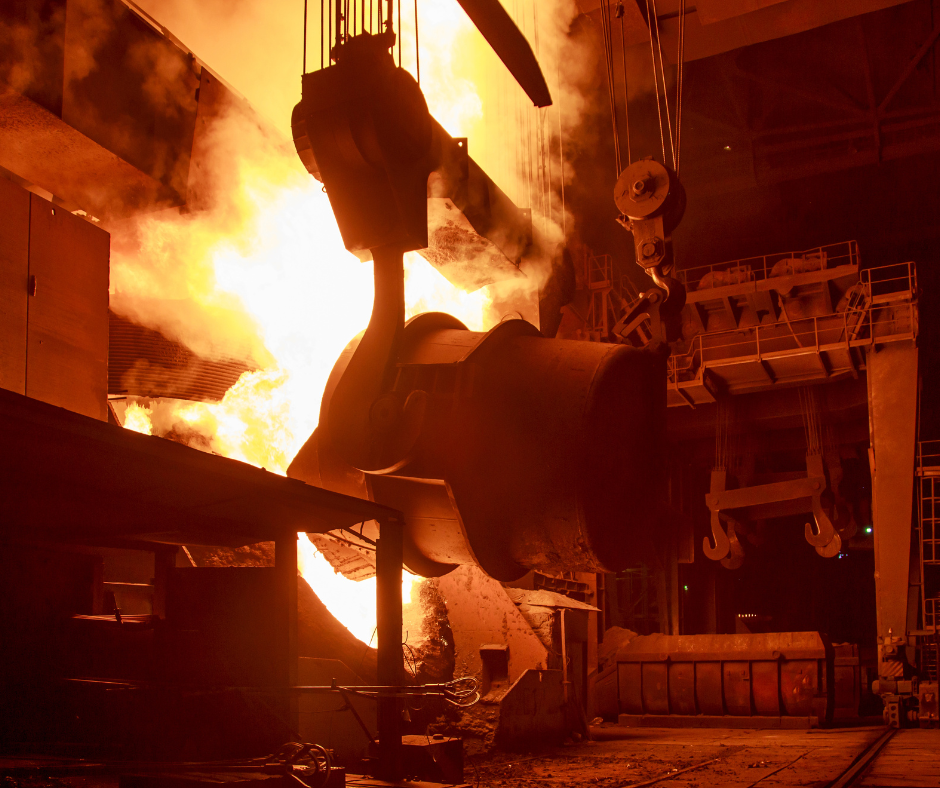
The Basic Oxygen Furnace (BOF) is a cornerstone in the steelmaking industry, playing a vital role in converting raw iron into high-quality steel. Central to this process is the use of oxygen, which is introduced into the molten iron to remove impurities and reduce carbon content. This method, known as basic oxygen steelmaking, is highly efficient and produces steel that meets the rigorous standards required in industries such as construction, automotive, and manufacturing.
How Is Oxygen Used in the Basic Oxygen Furnace?
In the Basic Oxygen Furnace, oxygen is the key agent responsible for refining the molten iron. The process begins with charging the furnace with raw materials, primarily molten pig iron from a blast furnace and scrap steel. Once the furnace is charged, pure oxygen (about 99.5% purity) is blown into the molten iron through a water-cooled lance at supersonic speeds. Here’s how oxygen transforms the iron:
- Oxidation of Carbon:
- Oxygen reacts with carbon present in the molten iron to form carbon monoxide (CO) and carbon dioxide (CO2). This oxidation reaction reduces the carbon content, which is essential for converting iron into steel.
- Removal of Impurities:
- The oxygen also reacts with other impurities, such as silicon, manganese, and phosphorus, oxidizing them and allowing these unwanted elements to be removed. The oxidized impurities combine with lime (added as a flux) to form slag, which floats on top of the molten steel.
- Heat Generation:
- The oxidation reactions are highly exothermic, meaning they release a significant amount of heat. This heat helps maintain the temperature of the molten metal, ensuring it remains in a liquid state throughout the process.
The Role of Oxygen in Steelmaking
Oxygen is crucial in steelmaking for several reasons:
- Purification: Oxygen purifies the iron by reducing its carbon content and removing other impurities that could weaken the final steel product.
- Efficiency: The use of oxygen allows for the rapid processing of large quantities of iron, making the Basic Oxygen Furnace an efficient method for steel production.
- Quality Control: By controlling the oxygen flow and the reactions it triggers, steelmakers can precisely control the chemical composition of the steel, ensuring it meets specific standards for different applications.
How the Basic Oxygen Furnace Process Works
The BOF process is a series of carefully controlled steps that utilize oxygen to refine raw iron into steel:
- Charging the Furnace:
- The process starts with charging the furnace with molten pig iron and scrap steel.
- Blowing Oxygen:
- Pure oxygen is blown into the furnace through a lance, initiating the oxidation of carbon and impurities.
- Formation of Slag:
- The oxidized impurities form slag, which is skimmed off the surface, leaving purified molten steel.
- Tapping the Steel:
- Once the desired chemical composition is achieved, the molten steel is tapped into a ladle for further processing or casting.
- Secondary Refining:
- After tapping, the steel may undergo additional treatments to adjust its properties before it is cast into the desired shapes.
Advantages of Using Oxygen in Steelmaking
- Speed and Efficiency: The introduction of oxygen significantly speeds up the steelmaking process, allowing for large-scale production in a short time.
- Cost-Effectiveness: Using oxygen in the BOF process reduces the need for external heat sources, making the process more energy-efficient and cost-effective.
- Environmental Benefits: The BOF process allows for the recycling of steel scrap, reducing the need for raw materials and lowering the environmental impact of steel production.
Challenges and Considerations
While the use of oxygen in steelmaking offers many benefits, it also presents some challenges:
- Control of Reactions: The oxidation reactions must be carefully controlled to prevent over-oxidation, which could lead to defects in the steel.
- CO2 Emissions: The process generates carbon dioxide, a greenhouse gas, necessitating measures to mitigate its environmental impact.
The Future of Oxygen in Steelmaking
As the steel industry evolves, the role of oxygen in steelmaking is likely to expand:
- Carbon Capture Technologies: Innovations in carbon capture and storage (CCS) are being explored to reduce the CO2 emissions generated during the BOF process.
- Enhanced Process Control: Advances in automation and sensor technology are improving the precision of oxygen delivery, leading to even higher-quality steel production.
Conclusion
The Basic Oxygen Furnace (BOF) is a vital technology in modern steelmaking, with oxygen playing a central role in refining iron into steel. By understanding how oxygen is used in this process, we can appreciate the efficiency, quality, and innovation that make steel one of the most essential materials in the world today. As technology continues to advance, the use of oxygen in steelmaking will likely see further enhancements, driving the industry toward more sustainable and efficient production methods.
For over 80 years, Metro Welding Supply Corp has been the trusted partner for businesses across Southeast Michigan, delivering high-quality welding supplies, specialty gases, and exceptional customer service. Whether you’re in construction, manufacturing, or healthcare, we have the products and expertise to meet your needs. Our team is committed to providing reliable solutions that keep your operations running smoothly. Contact us today at 313-834-1660 or via email at sales@metrowelding.com to learn how we can support your business with the best in welding supplies and specialty gases.
How is oxygen used in a Basic Oxygen Furnace?
Oxygen is blown into the molten iron to oxidize and remove carbon and other impurities, transforming the iron into steel.
Why is oxygen important in steelmaking?
Oxygen is crucial for purifying the iron, reducing its carbon content, and controlling the final composition of the steel.
What are the environmental impacts of using oxygen in steelmaking?
The process generates CO2 emissions, which are a concern for greenhouse gases. However, efforts are being made to reduce these emissions through advanced technologies.
Can the BOF process use recycled materials?
Yes, the BOF process can incorporate a significant amount of scrap steel, making it both cost-effective and environmentally friendly.
What is the future of oxygen use in steelmaking?
The future will likely see improvements in carbon capture, process control, and efficiency, making the use of oxygen in steelmaking even more sustainable.
Ready to work with Metro Welding Supply Corp.?
Let's connect! We’re here to help.
Send us a message and we’ll be in touch.
Or give us a call today at 313-834-1660